T-FLEX Технология — от САПР ТП к комплексной системе технологической подготовки производства
Автор: Нина Гордеева, менеджер продукта T-FLEX Технология компании «Топ Системы»
Технология — мост, по которому изделия переходят «из мира идей в мир вещей». Задача технологической подготовки производства — построить оптимальный мост максимально быстро и недорого.
Системы автоматизированного проектирования технологических процессов (САПР ТП), или, как сейчас модно называть на западный манер, CAPP (Computer Aided Process Planning), имеют глубокие российские корни. Основа успешного развития систем проектирования технологических операций лежит в стандартизации представления технологических процессов (ТП) и методов их разработки для всей, тогда еще советской, промышленности. Зарубежные компании не имели такого уровня стандартизации описания ТП. Возможно, это вызвано эффектом «поклонения» коммерческой ценности know-how и опасения за возможную утечку знаний на конкурентные производства. Появившиеся гораздо позднее принципы «бережливого производства» призваны задавать вектор и прививать философию совершенствования процессов предприятия, в том числе и технологических процессов. При этом они не регламентируют четкой по-следовательности действий, как, в какое время и в каких ситуациях применять эти самые принципы «бережливого производства». Однако формализация технологических документов в зарубежных компаниях активно внедряется на основе решений предлагаемых разработчиками систем CAPP. Необходимо отметить, что современные западные системы CAPP создаются преимущественно для сборочных производств. Замечено, что западные разработчики активно используют российский опыт создания САПР ТП: принципы построения систем, формализация отчетных форм, имеющих много схожих черт с технологическими картами по ЕСТД[1]
За 35 лет развития отечественных САПР ТП многое изменилось. Изначально системы создавались для автоматизации формирования стандартного комплекта технологической документации и выполнения некоторых расчетов. В 2000-х широкое распространение принципов PLM в России привело к кардинальному пересмотру задач, решаемых САПР ТП. На сегодняшний день система технологической подготовки производства должна не только удовлетворять потребности разработчиков технологических процессов (технологов) и нормировщиков по выпуску документации в соответствии с ЕСТД, но и:
- использовать данные, полученные на более ранних этапах подготовки производства (преимущественно конструкторские данные);
- позволять использовать электронные ТП как нормативные данные для планирования ресурсов предприятия, оперативного планирования и учета производства;
- обеспечивать пользователей инструментами коллективного взаимодействия в рамках единого информационного пространства предприятия или группы предприятий, с обеспечением регламентированного доступа пользователей к различным данным;
- поддерживать единство, непротиворечивость и актуальность хранимых данных;
- встраиваться в систему электронного документооборота предприятия с применением бизнес-процессов и электронных подписей;
- поддерживать тесную связь с системой планирования, так как технологическую подготовку производства тоже нужно планировать и управлять ею;
- взаимодействовать с различными прикладными приложениями и модулями, которые решают узкоспециализированные задачи (CAD/CAM-системы, системы раскроя, расчетные модули и т.д.).
Таким образом, на смену малофункциональным локальным приложениям САПР ТП пришли клиент-серверные приложения, способные решать все вышеперечисленные задачи самостоятельно или в режиме интеграции с другими приложениями. Таким приложением является T-FLEX Технология[2]. В большинстве случаев технологическая подготовка производства (ТПП) представляет собой последовательность трех основных этапов: этап директивного (предварительного) проектирования, этап проектирования технологических процессов и оснащения, этап управления изменениями.
На схеме, приведенной на рис. 1, отражено, что технологическая подготовка производства (в общем случае) распараллелена с другими процессами предприятия. Сигналом для начала процесса ТПП служит завершение технологического контроля[3], а именно — окончательно приняты все конструктивные решения.
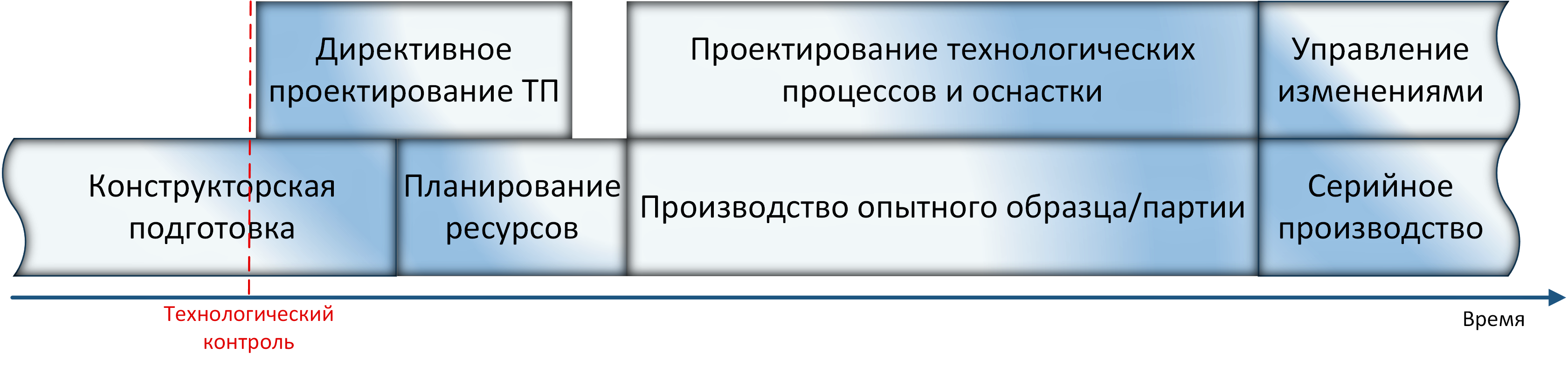
Рис. 1. Схема технологической подготовки производства
Этап директивного проектирования
Этап директивного проектирования включает описание технологической структуры изделия, определение маршрута (расцеховки) изготовления с определением укрупненных временных нормативов по цехопереходам, материальное нормирование с расчетом и назначением заготовок.
Оперативное решение этих задач в рамках ТПП является ключевым фактором для обеспечения эффективного, а именно экономически целесообразного производства. Полученные на этом этапе данные позволяют сформировать перечень производственных потребностей и провести оценку и планирование ресурсов, а значит, на ранних этапах реализовать планирование производства и закупок с высокой степенью точности.
Данное направление развития для систем ТПП является достаточно молодым. В современных системах можно встретить перечисленную функциональность, но, как правило, она не носит системного характера. Компания «Топ Системы» в рамках развития продукта T-FLEX Технология ведет активную работу по наращиванию функциональных возможностей в направлении директивного проектирования. В настоящее время реализованы такие механизмы, как работа со структурами изделий (в том числе, описание техно-логической структуры изделия и использование ее при дальнейшем проектировании ТП), определение маршрутов изготовления изделий (в том числе альтернативных) с указанием укрупненных нормативов времени, материальное нормирование и назначение заготовок, поэлементный просмотр применяемости. При этом уже реализованная функциональность постоянно развивается с учетом предложений пользователей, которые используют ее при подготовке реального производства. По функционалу работы с технологической структурой изделия мы активно развиваем механизмы, обеспечивающие иерархические взаимосвязи структур между собой, инструменты сравнения и отслеживания изменений относительно конструктивной структуры, механизмы автоматизированного создания объектов технологической структуры (например, при нормировании основного материала для детали и подборе заготовки в ее технологической структуре автоматизированно может формироваться объект типа «Заготовка» с рассчитанными параметрами).
В случае материального нормирования к уже реализованной функциональности по расчету заготовок из стандартного сортамента добавится новая функциональность, позволяющая рассчитывать нормы расхода основных материалов на заготовки, полученные различными технологиями литья и обработки давлением. Помимо расчетов основных материалов активно развивается функционал по расчету вспомогательных материалов (например, покрытий или сварочных материалов).
Сегодня на повестке дня стоит задача автоматизации анализа конструкции на технологичность, которая относится к одной из задач технологического контроля. Модуль анализа должен включать ряд решений, позволяющих на основе огромного объема накопленных данных по конструкциям и составам изделий для каждой новой конструкции решать следующие задачи:
- анализировать применяемость с определением степени унификации деталей и сборочных единиц (ДСЕ). Эти данные могут быть использованы при оценке экономической целесообразности производства изделия. Увеличение степени унификации применяемых ДСЕ значительно сокращает трудозатраты на дальнейшую подготовку производства, а кроме того, снижаются экономические риски, связанные с производством уникальных ДСЕ;
- ускорить подбор ДСЕ-аналогов, которые уже изготавливались или закупались. Это позволит значительно ускорить технологическую подготовку производства за счет быстрого подбора технологий-аналогов или формировать предложения по доработке конструкции с целью увеличения коэффициента унификации;
- получать перечень уникальных узлов и деталей, который должен стать основой для автоматизированного формирования плана и реальной оценки трудоемкости подготовки производства.
Решение перечисленных задач значительно углубит этап директивного проектирования в сторону начала конструкторской подготовки производства и расширит сферу влияния системы ТПП в рамках PLM.
Этап проектирования технологических процессов и оснащения
На сегодняшний день разработка технологических процессов в системе T-FLEX Технология может проходить с использованием различных подходов:
- единичная, типовая, групповая;
- с использованием прототипов и аналогов;
- маршрутная, маршрутно-операционная, операционная.
На этом этапе технологическая подготовка производства заключается в описании технологических операций, за счет чего дополняются и уточняются ранее полученные данные (маршрут, технологический состав, нормы). За последнее время мы значительно продвинулись в направлении сборочных ТП (рис. 2), типовых ТП (рис. 3), описания операций ЧПУ (рис. 4). В T-FLEX Технологии реализованы принципы параметризации с поддержкой ассоциативной связи на эскизы, чертежи и модели, выполненные в системе конструкторского проектирования T-FLEX CAD[4]. В дополнение к перечисленной базовой функциональности могут поставляться модули нормирования: «Трудовое нормирование», «Режимы резания», «Дуговая сварка в среде защитных газов», «Лакокрасочные покрытия», «Материальное нормирование».
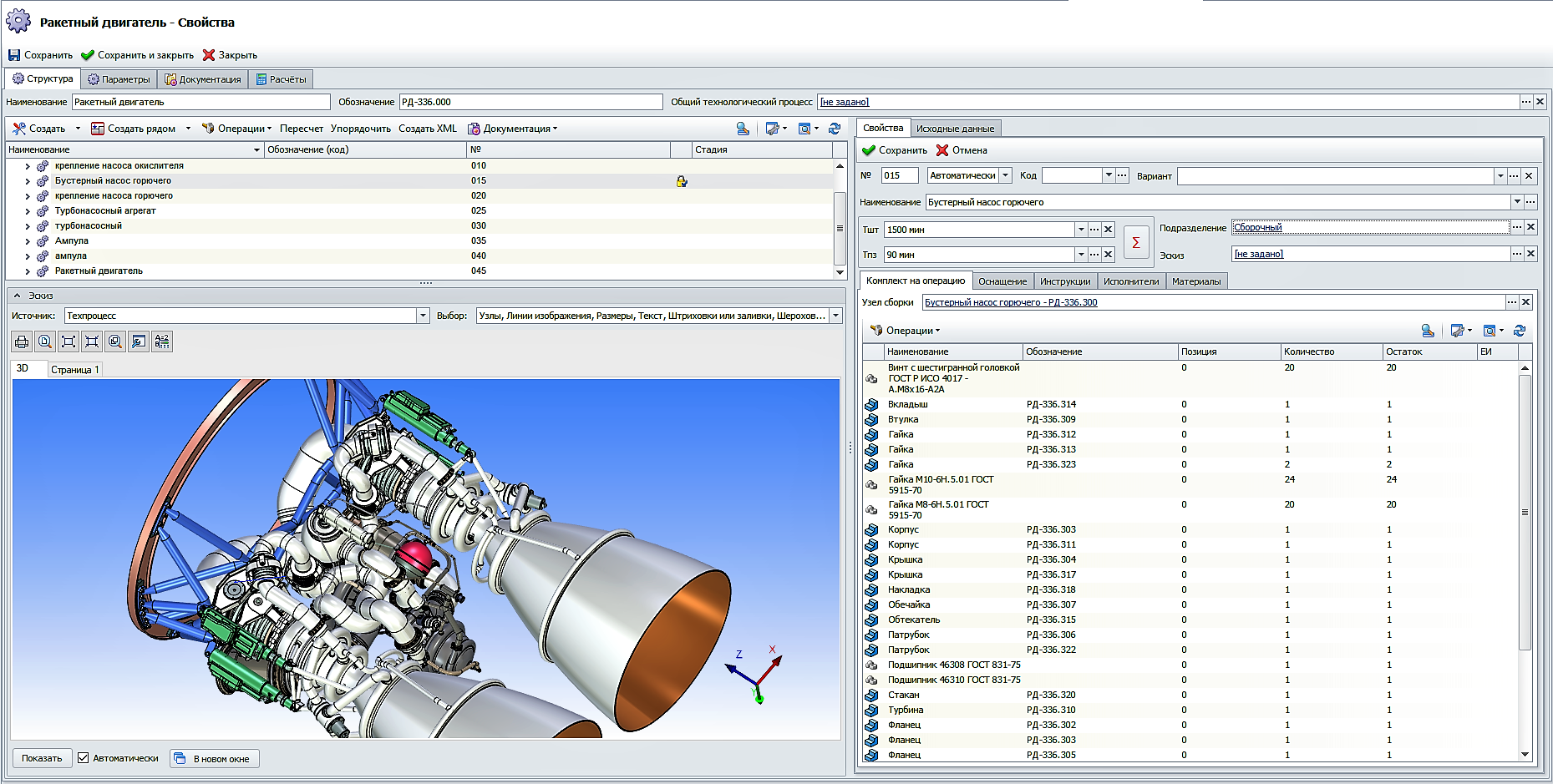
Рис. 2. Сборочный технологический процесс в T-FLEX Технология
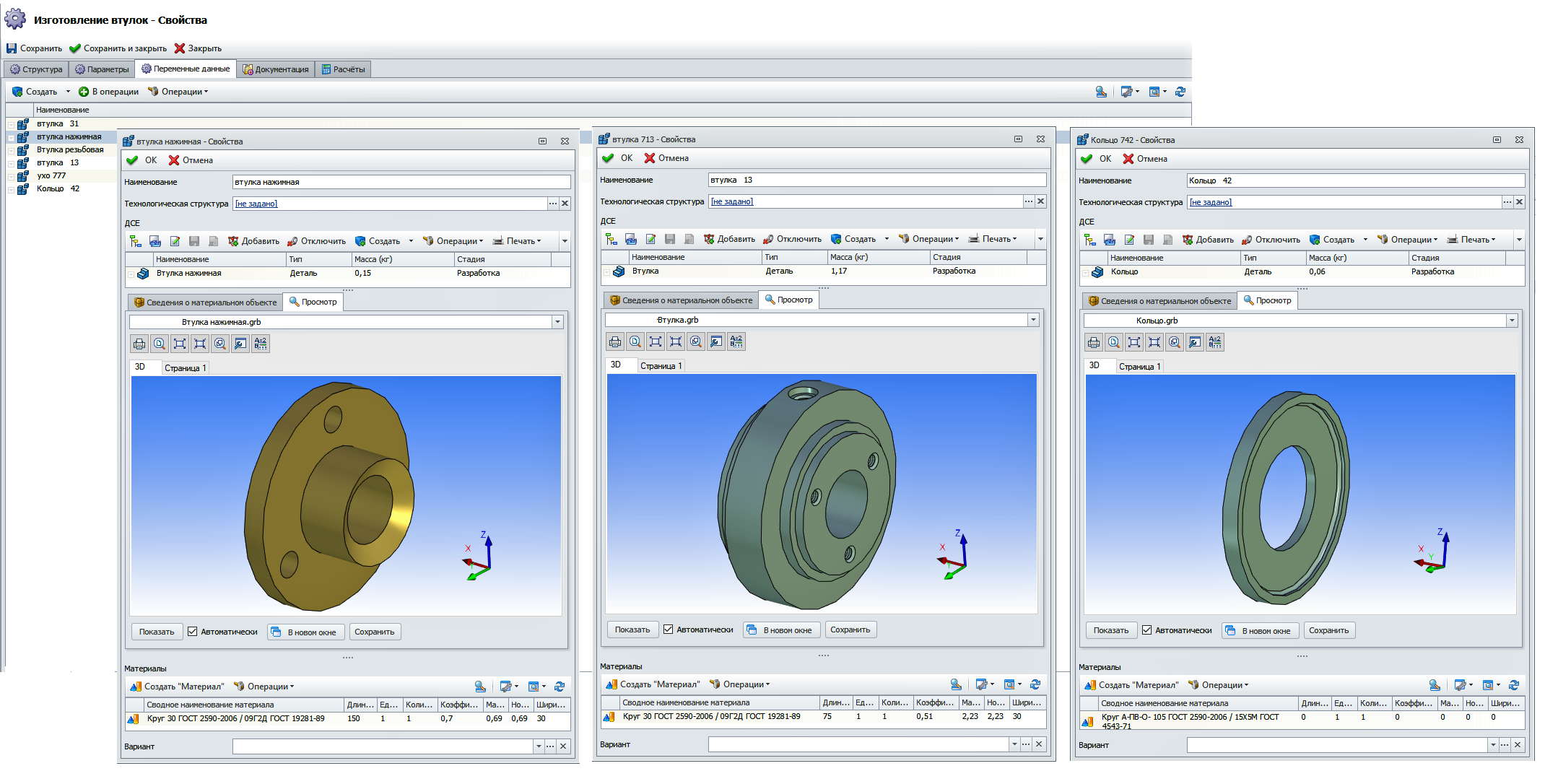
Рис. 3. Типовой технологический процесс в T-FLEX Технология
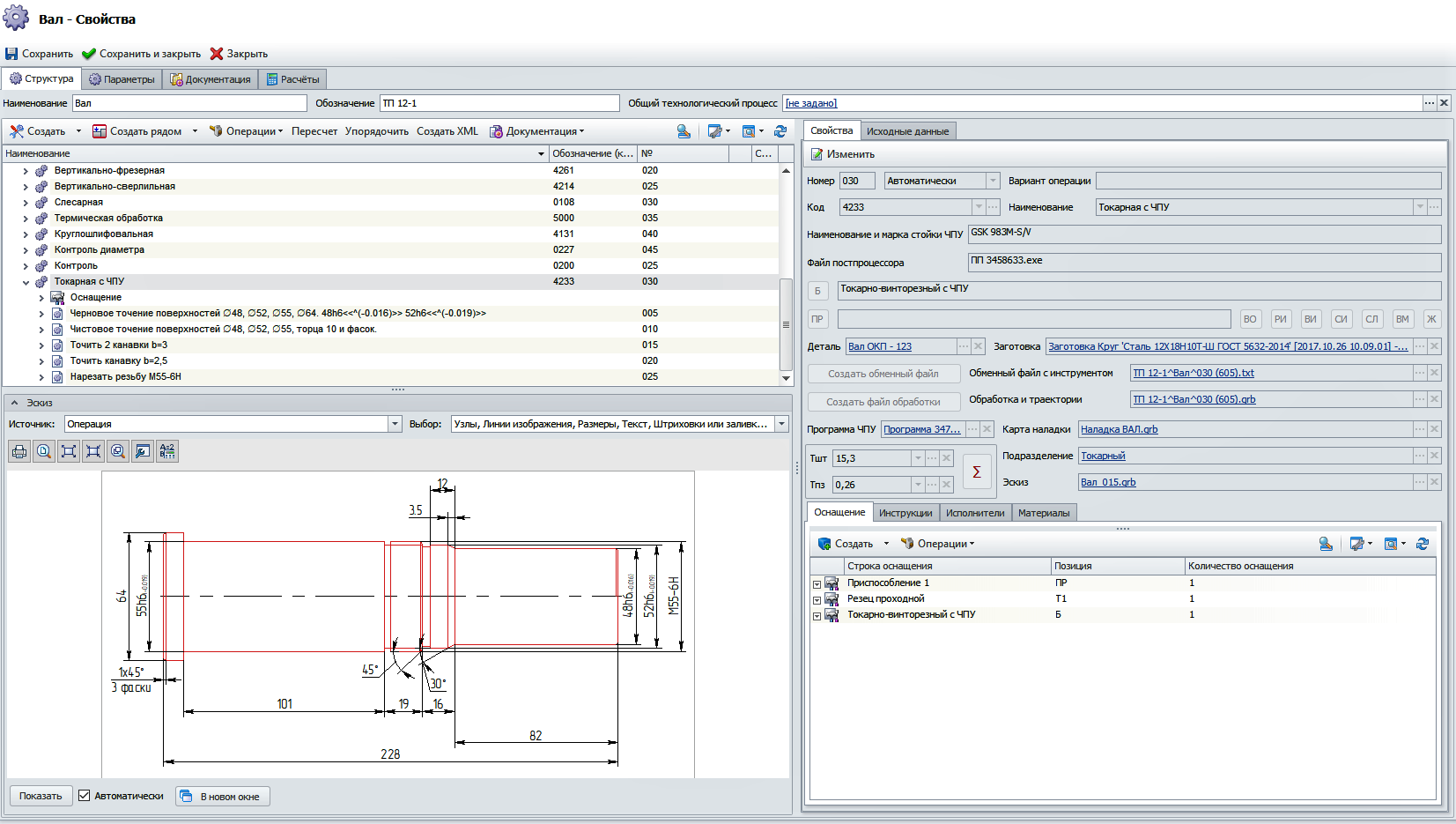
Рис. 4. Операция ЧПУ в T-FLEX Технология
При этом T-FLEX Технология от версии к версии не теряет, а только наращивает свою гибкость, что позволяет выполнять структурные модификации (создание справочников, связей, типов, диалогов ввода и др.), не прибегая к инструментам программирования. Это означает, что T-FLEX Технология легко настраивается под любой, даже самый специфичный тип производства, и с этой задачей может справиться не только администратор системы, но и среднестатистический технолог.
Необходимость в проектировании и изготовлении нестандартного оснащения определяется на основе анализа уникальных узлов и деталей, которые предстоит изготавливать. В технологической структуре изделия существует возможность включать объекты с типом «технологическое оснащение», которые необходимо спроектировать и изготовить. Впоследствии эти данные можно использовать при планировании работ и затрат по производству нестандартного оснащения. Сам же процесс проектирования оснащения осуществляется в системе T-FLEX CAD под управлением T-FLEX DOCs.PDM.[5]
Этап управления изменениями
Управление изменениями — это системный подход по переводу объекта из текущего состояния в желаемое будущее состояние.
Задача управления изменениями — одна из самых труднореализуемых в рамках электронного технического документооборота. Для ее решения в T-FLEX DOCs используется целый набор ключевых функций:
- версии и варианты для управления текущим, всеми прошлыми, будущими и временными состояниями объектов;
- бизнес-процессы для описания и выполнения устойчивых схем процессов согласования и последовательного выполнения автоматизированных процедур;
- доступы обеспечивают разрешение и запрет на определенные действия со стороны пользователей в зависимости от различных условий;
- стадии определяют этап жизненного цикла электронного объекта (разработка, согласование, хранение, корректировка, аннулировано);
- генератор отчетов для автоматизированного формирования документации (например, извещений об изменении в соответствии с ГОСТ 2.503).
Хочется отметить, что выпуск извещения об изменении не является целью управления изменениями — это только одна из сопутствующих функций. Основная цель — обеспечить информационную поддержку жизненного цикла изделия средствами PLM-системы предприятия. При этом электронная модель изделия состоит не только из набора конструктивных данных, но и из технологических данных, изменение которых оказывает непосредственное влияние на все последующие процессы, связанные с производством изделий.
Обширный круг задач технологической подготовки производства и ее ключевая роль в переходе от конструкторского проекта к реальному производству изделий только подчеркивают важность и необходимость автоматизации этого процесса. С момента выпуска первой версии, более 15 лет назад, T-FLEX Технология прошла долгий путь от САПР ТП до комплексной системы технологической подготовки производства и продолжает развиваться. Постоянно расширяется круг решаемых задач, а уже готовые проверенные решения развиваются в части быстродействия и эргономики. В своей работе над системами мы исходим из того, чтобы максимально освободить человека от повторяющихся рутинных задач и высвободить ему время для принятия более обоснованных взвешенных решений и инженерного творчества.
- ↑Единая система технологической документации — комплекс стандартов и руководящих нормативных документов, устанавливающих взаимосвязанные правила и положения по порядку разработки, комплектации, оформлению и обращению технологической документации, применяемой при изготовлении и ремонте изделий.
- ↑Входит в программный комплекс T-FLEX PLM, является конфигурацией приложения T-FLEX DOCs.
- ↑Цели, задачи, содержание и порядок проведения технологического контроля регламентируются ГОСТ 14.206.
- ↑T-FLEX CAD — система автоматизированного проектирования, обладающая всеми современными средствами для разработки изделий любой сложности. Программа объединяет мощные параметрические возможности трехмерного моделирования со средствами создания и оформления конструкторской документации.
- ↑T-FLEX DOCs.PDM — система, которая предоставляет инструменты для управления структурами изделий, ведения номенклатуры, проведения извещений об изменениях, формирования спецификаций и проведения прочих действий, связанных с конструкторской подготовкой производства.
Дополнительно
Поделиться ссылкой: